101 Series: To Splice or Not to Splice
August 8, 2018 / General, 101 learning, Installation and testing, Upgrading and troubleshooting, Best Practices
Fiber splicing is a method of connecting two fibers, whereby two fibers are precisely cleaved and then aligned and fused using a fusion splicing machine. The fusion of two fibers is achieved by an electric arc that essentially welds the fibers together. A mass fusion splicer welds 12-fiber together at once and is performed using 12-fiber ribbon cable.
Whether you’re new to fusion splicing, or simply curious as to why one would choose to splice over using preterminated fiber cabling or other field termination methods, we thought it would be good to take a look at applications and scenarios where splicing makes sense and key considerations.
When and Where
Fusion splicing provides the lowest loss and least reflectance, and is considered the strongest and most reliable method of joining fibers. When properly executed, a splice can exhibit a loss of less than 0.1dB. In contrast, fiber connectors will typically yield a loss of 0.2dB or higher. Since insertion loss is the primary performance parameter required to certify a fiber link, and high speed 40 and 100 Gig fiber applications have more stringent loss requirements, fusion splicing has grown in popularity.
Fusion splicing is often used for repairing a broken fiber link, and it is considered the best method for connecting 250-micron outside plant fiber to 900-micron inside plant fiber at the building entrance. Fusion splicing can also be used for creating fiber links within the data center or in the LAN. Fusion splicing at the building entrance or at fiber panels can be achieved using splice-on pigtails or splice-on connectors.
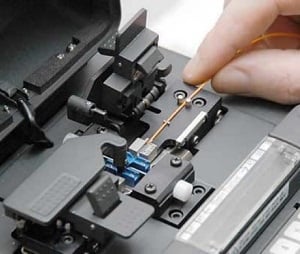
Splice-on pigtails are pre-polished connectors with a short (typically 5 meters or less) fiber stub that is fused to the incoming fiber. The splices are then protected within a splice sleeve, which is a transparent tube that is typically surrounded by a heat-shrinkable outer tube along with some type of strength member. Splices within their sleeves are stored in splice trays along with any slack fiber.
Instead of splicing to a pigtail stub, splice-on connectors include a pre-polished ferrule and fiber with a much shorter fiber stub housed within the protective sleeve of a connector. Once the incoming fiber is stripped, cleaved and fused to the fiber stub, the connector body is assembled around the ferrule. One of the key benefits of a splice-on connector versus the pigtail is that is doesn’t require the protective splice sleeve and splice tray for storage.
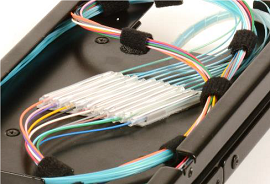
When it comes to applications that require multifiber MPO connectors, most deployments will use preterminated MPO cables that are factory terminated and tested. While preterminated MPOs are available with losses as low as 0.2dB, and they are plug-and-play for fast deployment, they require longer lead times since they are made to order. Preterminated cables also tend to carry higher material costs and require link lengths to be carefully predetermined—ending up with cables that are too short can cause significant delay while cables that are too long require storing and managing slack.
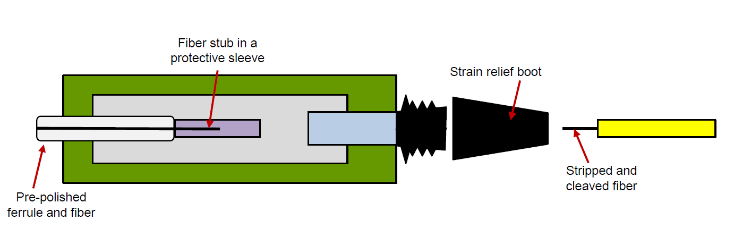
While duplex connectors (such as LC, ST or SC style connectors) can be field terminated using mechanical crimp methods or traditional epoxy-polish, the only option for MPO field termination is fusion splicing with splice-on MPO pigtails or splice-on MPO connectors. Hence, these may be the best choice when link lengths can’t be predetermined or longer lead times are not an option.
Some Considerations
While fusion splicing is optimal for certain applications and situations, there are some considerations. First and foremost, fusion splicing requires a fusion splicer—and they are not exactly inexpensive. If you own or have access to a splicer, you’re one step ahead of the game. But if you’re going to purchase a fusion splicer, you want to make sure that you’ll be doing enough splicing to get your return on investment. Renting a splice machine is also an option if you’re not planning to do a lot of splicing.
Another cost to consider is the cleaver. Performance of a splice is highly dependent on the quality of the cleave, so a high precision cleaver is recommended. These are also not exactly inexpensive, but if you are doing any type of fiber field termination such as mechanical crimp or epoxy-polish, you likely already have a precision cleaver.
Compared to preterminated solutions that are quick and easy to deploy, fusion splicing does take more time, but with no lead times and no need to predetermine lengths, it can ultimately be faster. Fusion splicing also requires a good, solid work space. And when using splice-on pigtails, you want to be careful to properly manage your splices and slack within splice trays to prevent exceeding the bend radius of the fiber.
When it comes to troubleshooting splices, only an OTDR can tell you where a splice is located. But if you have a good quality splice with extremely low loss, you may need to adjust your OTDR loss threshold low enough to see these minor events. It’s also important to troubleshoot splices in both directions to get the actual loss since a mismatched splice could result in negative loss in one direction and too much loss in the other. That is precisely why bidirectional testing is required in Tier 2 testing. Thankfully, Fluke Networks’ OptiFiber® Pro features a built-in SmartLoop Assistant that makes bidirectional testing easy and its Loss Threshold can be user defined from 0.01 to 1.50dB.